The plate type air-to-air heat exchanger made of polymer PP (polypropylene) material is a heat exchange device based on polypropylene material, mainly used for heat exchange between gases. Here are its main features and application areas:
Main features:
Corrosion resistance: PP material has strong chemical corrosion resistance and is suitable for acidic or alkaline gas environments, especially performing well in industrial environments with strong corrosiveness.
Lightweight: Compared to metal heat exchangers, PP material heat exchangers are lighter in weight, making them easier to install and maintain.
Good thermal stability: Polypropylene has good thermal stability and can typically operate within a temperature range of -10 ° C to+95 ° C.
High cost-effectiveness: Due to the low cost of PP material and relatively easy processing, the overall cost is relatively economical.
Environmental friendliness: Polypropylene is a recyclable polymer material with minimal impact on the environment after disposal.
Main application areas:
Chemical and pharmaceutical industries: used for heat recovery or temperature regulation of corrosive gases.
Exhaust gas treatment system: During the air purification process, heat is recovered from harmful gases through a heat exchanger.
Food processing: In some food production processes, it is used for gas exchange to maintain the stability of environmental temperature.
HVAC system: Used in the ventilation and air conditioning systems of buildings for air preheating or pre cooling, improving energy efficiency.
The plate type air-to-air heat exchanger made of polypropylene material has become an ideal choice for many specific industrial fields due to its unique corrosion resistance and good cost-effectiveness.
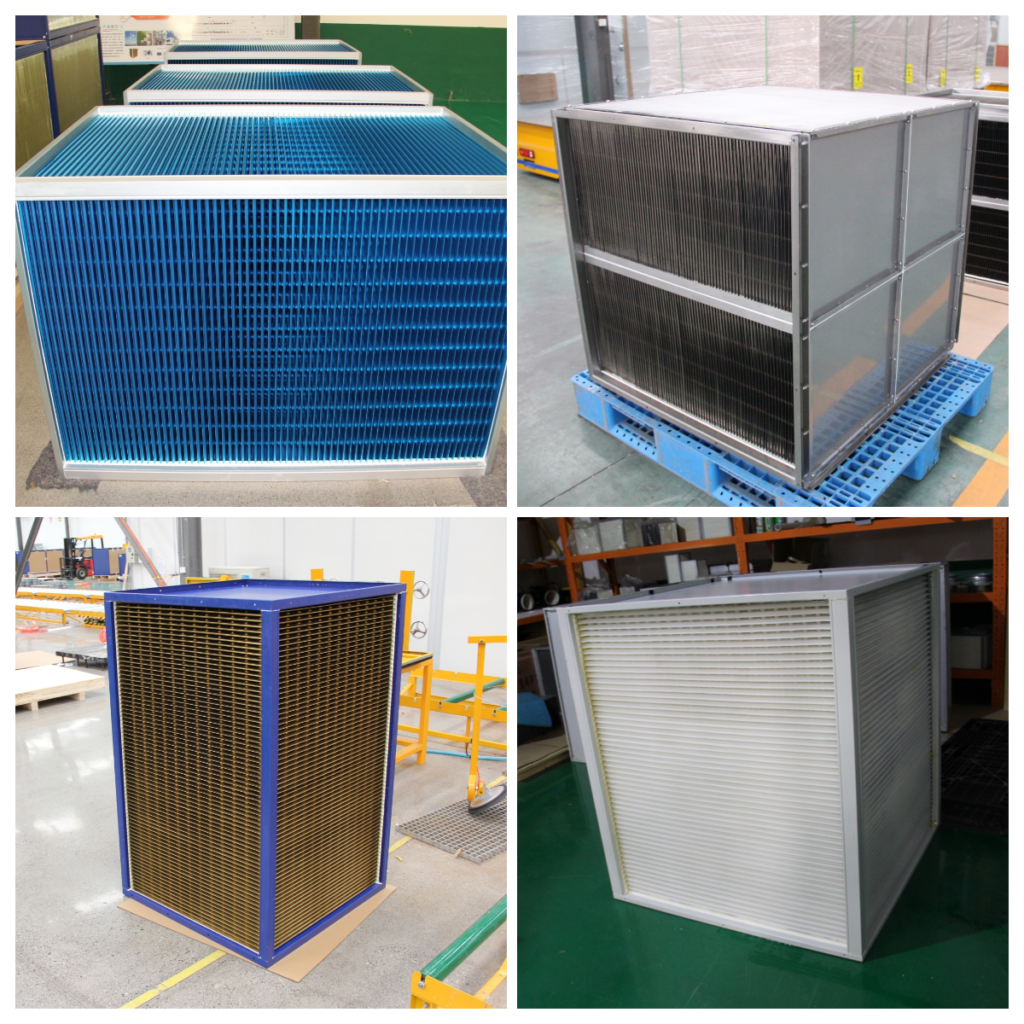