Spray coating is a surface treatment method that sprays plastic powder onto parts, widely used in various fields such as automotive, electronic products, furniture and appliances, construction industry, machinery, and public facilities. The waste heat recovery plate heat exchanger for spray coating waste gas is an energy recovery device that can recover and utilize the heat energy generated during the high-temperature baking process of spray coating.
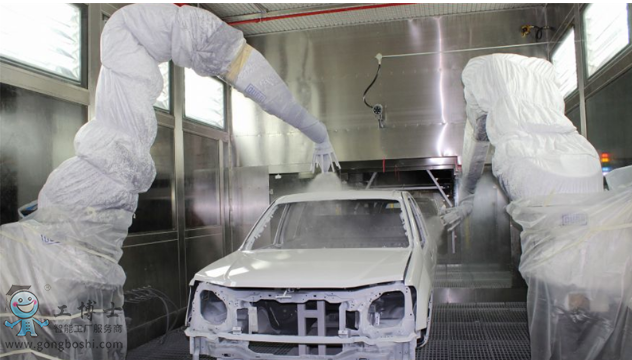
working principle:
The plate heat exchanger for waste heat recovery from spray coating waste gas transfers the heat from the dry waste gas to other media, such as fresh air or water, to achieve energy recovery and utilization. The device consists of a series of parallel arranged metal plates, and the gas from the heat source and cold source flows cross between the plates, achieving heat transfer through thermal conduction and convective heat transfer of the metal plates.
Application areas:
Spray painted waste gas heat recovery plate heat exchangers are widely used in industries that require a large amount of thermal energy, such as metallurgy, chemical industry, building materials, machinery, electricity, etc. In these industries, the exhaust and smoke exhaust of various smelting furnaces, heating furnaces, internal combustion engines, and boilers, as well as the residual heat of flue gas from industrial kilns, are the main objects of waste heat recovery.
Product advantages:
Efficient heat transfer: The plate type gas waste heat recovery heat exchanger adopts an efficient plate design with a high total heat transfer film coefficient, which can quickly and effectively transfer heat.
Compact structure: The equipment occupies a small area, is lightweight, and has a large heat exchange area per unit volume, making it suitable for situations with limited space.
Safe and reliable: The equipment adopts a fully welded form, and the manufacturing process strictly follows the enterprise standards. Multiple pressure testing procedures ensure that the equipment can be used for a long time without leakage.
Energy saving and environmental protection: By using heat exchange to cool down the waste heat flue gas, the heat recycling system achieves the goal of energy saving, improves the economic efficiency of the enterprise, and reduces operating costs.
matters needing attention:
When selecting and using spray coating waste gas heat recovery plate heat exchangers, it is necessary to design and install them according to specific spray coating process parameters and requirements. It is important to ensure that the selection of the heat exchanger is appropriate, the material is heat-resistant, and appropriate control measures are taken to ensure the stability and safety of the heat exchange process.